In an optical encoder, very small LEDs are used to transmit light through a disk with notches at specified intervals. These intervals determine the resolution of the encoder. Once the light passes through the notches, light sensitive receivers receive the signal and send it out as position data.

AMT encoders can be described in a similar manner; but instead of transmitting light via LEDs, an electrical field is transmitted. In the place of an optical disk is a PCB rotor containing a metal trace sinusoidal pattern that modulates the electrical field. The receiving end of the modulated signal is then passed back to the transmitter where it is compared against the original via a proprietary ASIC. Performance of the ASIC is boosted further in many AMT products with the coupling of an onboard MCU. Because of this design, the AMT capacitive encoder allows for a much higher range of accuracy and flexibility compared to other encoders on the market. The rotor PCB is designed for a high resolution of position. This high base resolution allows the ASIC and the MCU to computationally derive a wide range of final resolutions that the customer may select for their solution. Because the resolution selection occurs in the ASIC and MCU, the customer needs only to purchase one part number, yet receives a product capable of many resolutions.
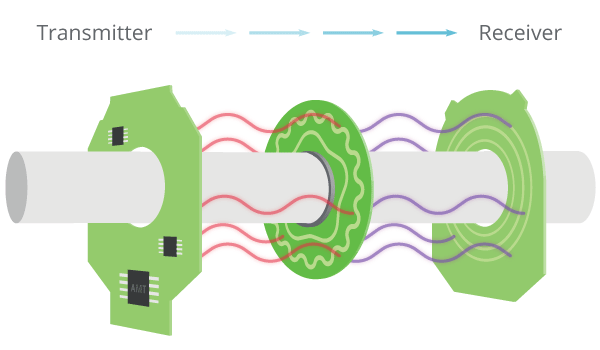
The outputs waveforms of an incremental AMT capacitive encoder have the same characteristics of any optical encoder, so the transition should be seamless. Every incremental AMT encoder has quadrature A/B signals as well as an index pulse. These are 5 V logic waveforms that are 90 degrees out of phase to indicate direction of rotation.
In fact, an AMT capacitive encoder may require even less external circuitry than an optical encoder. Many encoders use an open-collector output which leaves the output transistor’s collector floating (neither high nor low). To operate the encoder, you need a pull-up resistor to pull the signal to the supply voltage. The active output will then pull the signal down to switch the output pulses on and off to create the expected square waves. All AMT capacitive encoders use a CMOS push-pull drive that does not require external circuitry to create the expected square waves. The added benefit of a CMOS driven output is its compatibility with any type of input.
For more information on common encoder output signals, check out our blog post.
- Position values wrong
- Position values jumping around while stationary
- Encoder absolute position (index) drifting
- Wrong startup location
This is most likely indicative of physical wear in the encoder due to improper mounting. Hand rotate the device with the encoder mounted and listen for audible noise for confirmation. Other signs of physical contact during rotation include increased torque/current required for driving the motor, the encoder being hot to the touch, and laggy position readings. Damaged encoders should be discarded and replaced with new ones making sure to follow the proper .
We offer a range of standard incremental encoders, absolute encoders, and commutation encoders for brushless dc motors. Our AMT encoders are offered in radial and axial configurations with various output signal types, including: single ended, differential line driver, SSI, SPI, RS-485, and more. Ultimately, our AMT encoder line has a variety of options to meet the needs of almost any application.
The AMT encoder series is quite rugged thanks to the underlying technology. Optical encoders have two main drawbacks; durability and life expectancy. An optical disk is typically made of glass which must be handled very carefully and does not hold up well to any sort of shock or vibration. Furthermore, the signal will be compromised if dirt or particulates get on the disk and interfere with the light signal. Additionally, LEDs inside an optical encoder are susceptible to burn-out over time.
AMT encoders have neither of these problems. Because they use capacitive technology, they have no need for LEDs or line of sight. As long as the PCB rotor can rotate freely, the electrical field will pass from the transmitting side to the receiving side regardless of any non-conductive particulate matter in between. This means that dust, dirt, grime, or pretty much anything else you may find in an industrial environment will have no effect on an AMT encoder.
Without the need for a glass disk of an optical encoder, the AMT encoder is much more durable. A drop, vibration, or shock has a reduced effect. Further information regarding shock and vibration testing is available on the AMT datasheets.
AMT encoders do not have wear components meaning there is no limit on the number of rotations.
You can submerge and AMT encoder in a nonconductive fluid such as gear oil and it will operate just the same. Optical encoders do not work in oils because the light is blocked or distorted from the transmitting side to the receiving side. This failure is due to an optical encoder’s requirement for line of sight. Since the AMT capacitive encoder does not use line of sight optics and relies on an electromagnetic field, it makes it ideal for motor or gear assemblies that require the entire unit to be sealed in oil. Many optical encoder manufacturers will offer a seal that can be used on the shaft to block oil from entering the encoder, but this solution introduces another potential failure from wear over time.
All AMT encoders use a capacitive ASIC to generate the various output resolutions based on a fundamental sinusoidal pattern internal to the encoder. By changing the count on the sinusoidal pattern different resolution sets can be generated. The AMT10E series uses the existing AMT10 series package, but has a different sinusoidal pattern count. This pattern count has been increased by 2.5 times, which in effect also increases each resolution by 2.5 times. As a tradeoff of the higher resolution set, the maximum RPM limits have been reduced by 2.5 times. This extended version of the AMT10 encoder offers resolutions not possible in the standard version such as 1250 PPR, 2500 PPR, and 5120 PPR.
The AMT10 Series and AMT10E Series encoders use the same proprietary ASIC available on all AMT products but are unassisted by any sort of MCU for absolute position tracking. To compensate for the lack of absolute position tracking, a Hall Effect sensor is used to create the encoder’s index pulse. Without the Hall Effect sensor, the encoder would output 8 index pulses per revolution. This is due to the sinusoidal waveforms etched onto the encoder’s rotor board; there are 8 wavelengths, or lambdas (λ) for the AMT10 and 20 lambdas for the AMT10E. Both encoders interpret their rotational movement based on the capacitive sensors with that many cycles, or lambdas, per turn. To generate the index pulse, the Hall Effect signal is gated together with its nearest wavelength pulse to generate an index pulse once per turn instead of once per lambda.
When the encoder is mounted to a motor with a strong stray magnetic field flux, it is possible for the index pulse to become compromised. If the strong magnetic field is greater than 40 Gauss on the motor (usually stepper motors), it could influence the Hall Effect sensor. This will affect the gating of the eight wavelength pulses and could either create more or fewer index pulses per revolution than are expected.
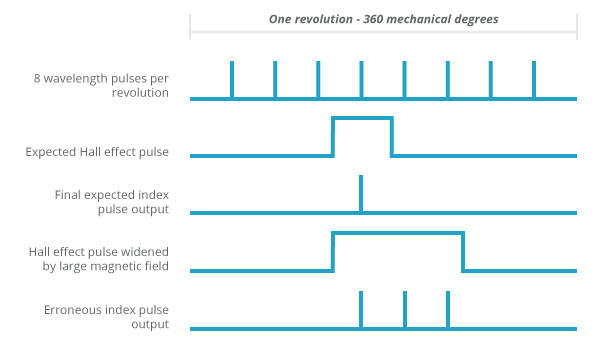
In this case, an AMT10 or AMT10E series encoder can be purchased without a magnetic Hall Effect sensor. In this configuration the index output from the encoder will occur 8 times per revolution, since there is no Hall Effect sensor gating, as shown above. As an alternative to the AMT10 or AMT10E series, the next-generation AMT11 Series incremental encoder utilizes an onboard MCU for generating the index pulse; this adds the bonus of allowing the user to zero-set index pulse at any angular position.
In some applications noise may leak into an AMT encoder via its cabling. To counter this noise the user should take care to ensure proper grounding at all locations. If noise is leaking in, it is suggested that the user try a shielded cable. The cable shielding can be grounded at the driver end, and then the encoder ground can be tapped into and grounded at the motor end. If the motor chassis needs to be isolated from the driver ground, the encoder may be capacitively grounded via a small electrolytic capacitor. If noise persists, Same Sky offers versions with a differential line driver, ideal for noisy environments and long cabling distances. Currently the AMT11, AMT13, AMT31, and AMT33 Series encoders are offered in various differential line driver output configurations for incremental and commutation outputs.
Using screws for mounting is recommended, but if you are mounting an AMT encoder in a location that cannot be drilled into, then an adhesive can be used. Any sort of glue or epoxy that is meant for use with plastic will be sufficient. However, we do suggest taking extra time to ensure proper alignment during installation with this method because it is not easily undone and adjusted. DO NOT use any type of adhesive tape.
AMT10 or AMT10E Series Encoders:
Each AMT10 or AMT10E encoder has a 4 position DIP switch on the backside. This allows the user to select from 16 resolutions just by adjusting which switches are on. See the AMT10 series or AMT10E series datasheet for the table of resolution options.
All Other AMT Series Encoders:
Using an AMT programming cable and a PC, Same Sky's AMT Viewpoint™ software allows users to configure several specifications depending on the series including: the resolution, direction of rotation, motor pole pairs, and zero position. Not sure what resolution you need? The AMT Viewpoint will help you decide with waveform plots and calculated pulse width values that automatically adjust when you select a resolution. All AMT encoders can also be custom ordered preconfigured to any available resolution.
When an encoder is rotating at near constant speed the output has no error. This is due to a design that incorporates what is best described as a moving average. This average helps stabilize by reducing the number of samples required to generate output. As the shaft rotates the current position is sampled at a designated rate and the speed is derived each time. This current velocity is stored into a register in the ASIC and is used to produce the output signals. As the encoder moves at constant speed, there will be no error, but if acceleration is introduced, this causes a slight latency in the time it takes the encoder to sample and recalculate velocity. The value caused by this latency is expressed as the position accuracy and is measured in degrees. As the ASIC measures changes in speed, it also measures the previous error value and uses that to compensate in the next correction that it makes. All of this happens very fast; the high accuracy for AMT encoders is typically around ±0.2 degrees; see encoder datasheets for exact numbers.
No, the encoder always starts up with the multi-turn counter at zero.
Single-turn encoders provide positioning data over one full revolution, 360°, with the output repeating for every revolution of the shaft. Multi-turn encoders also provide positioning data over a single turn but have an additional “turns” counter that measures the number of revolutions.
For more information on absolute encoders, read our blog post, "When is an Absolute Encoder Right for Your Design?"
Yes, we do have a few instructional videos:
Check out the following AMT Encoders resources:
- View mounting instructions, GUI download, and other AMT Resources
- Contact Us if you have additional questions